Squeeze cementing is basically a filtration process that occurs during the placement of the cement slurry into a wellbore entry point (casing leak, existing perforations, etc.) under sufficient differential pressure. The cement slurry is held in place until it cures and establishes a hydraulic seal.
Look at this picture in Squeeze Cementing Principles explaining the process involved.
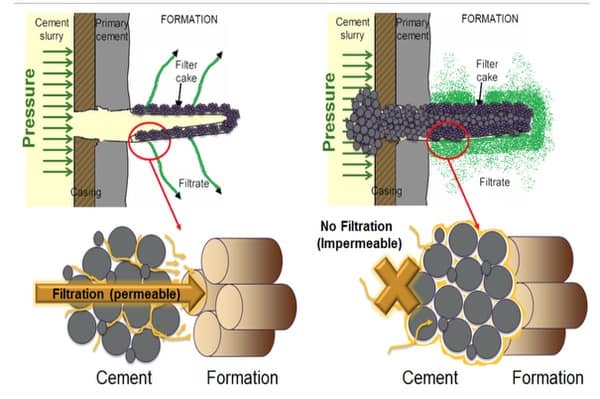
From the picture, squeeze cementing is achieved by forcing the cement slurry, under pressure, through leaks in the casing/wellbore to annular space. When the slurry is forced against a permeable formation, the solid particles filter out on the formation face as the cement filtrate enters the formation establishing a cement cake. Once set, the cement cake forms a nearly impermeable solid; at this point the objective of the squeeze cementing is achieved and isolation is restored.
Squeeze cementing hydraulic seal process:
• Differential pressure across the permeable formation
• Cement filtrate lost (filtration process)
• Cement filter cake build-up (solid particles filter out)
• Impenetrable solid cake formed.
Cement slurry selection
Successful squeeze cementing relies mostly on selecting the correct cement slurry to form an effective cement cake or node. Look at an example decision tree based on an injectivity test performed before the squeeze operation.
There are two main controlling variables during squeeze cementing that affect the rate of filtration, these are; the fluid loss of the cement slurry and the permeability of the formation. Prior to the squeeze cementing operation, an injectivity test is always performed, this injectivity is directly proportional to effective permeability using Darcy’s Law.

The fluid loss of the cement slurry is a property of the slurry that can be modified with chemicals (cement additives). This property is measured in the laboratory following the procedure in API RP 10B-2 / ISO 10426-2, and it is represented in ml per 30 minutes (ml/30min). This property is a measure of the “mobility” of the liquid phase (cement filtrate) inside the cement slurry (liquid cement = solids in reaction + liquid phase). The higher the cement slurry fluid loss, the higher the amount of liquid phase (cement filtrate) filtrating (being squeezed) to the formation. The objective is the creation of an impermeable cake or node; this is achieved when there is sufficient flow of cement filtrate from the cement slurry to the formation allowing for an accumulation of cement particles (cement cake) at the leak or porous media.
Squeeze Cementing techniques
There are two squeeze cementing techniques: cement plug and tool-assisted. These techniques are regularly used in combination with a Cast Iron Bridge Plug (CIBP). The CIBP is used to isolate the casing and any open perforated interval below the zone to be treated if required.
Advantages | Disadvantages | |
Cement plug -assisted | + Simple operation + Choice for long intervals + No need to squeeze/inject fluid ahead of the treatment fluid + No cement contamination in front of the leak/perforations just before squeeze + Easier drill out after cement setting + Running and hesitation squeeze are applicable. | + The whole casing is exposed to pressure and must be free of leaks + Pressure should be left trapped after squeeze to prevent backflow or damage on the cement cake + Typically limited to lower pressure squeeze + Casing expansion during treatment might close or diminish available flow paths behind the casing. These paths will later open once the pressure is released. |
Tool-assisted (Cement retainer) | + Shorter cement to be drilled inside the casing + Cement retainer can be set close to the target interval + Choice to prevent exposing casing to squeeze pressure + Pressure retained after squeeze while cement setting + More suitable for running squeeze procedure. | + Additional time required to set the cement retainer + Risks associated with the tool + Hesitation squeeze method is not advised + Lead cement interface is usually contaminated + Require fluid ahead or spacer to be injected + In cases of low injectivity there are additional risks. |
Cement plug – assisted squeeze
The preferred choice, because of its simplicity, is cement plug-assisted. This is mainly referred to in the literature as bradenhead squeeze (casing head is closed to prevent fluids from moving up the casing). It consists of the placement of a cement plug in front of the leak or perforations, POOH above the top of cement to apply pressure and squeeze the cement slurry.
This technique is normally used when there are no doubts concerning the capacity of the casing to withstand the squeeze pressure (in old wells, the casing pressure limits could be uncertain and normally safety factors must be considered). No special tools are involved; however, the cement plug must be stable and non-contaminated. Considerations for cement plugs are explained later in these posts (Balance Plug Calculations and Guidelines for Cement Plugs)
It is a simple method, no tool is required and the job execution is straightforward. It is essential that no part of the work-string be left in the cement during the application of squeeze pressure. The thickening and setting time of the cement slurry might shorten when subjected to pressure and filtration.
Tool – assisted squeeze
The main objective of using tools in squeeze cementing is to isolate the casing and wellhead while pressure is applied downhole. This feature typically allows for higher pressure during squeeze, when the casing condition is sub-standard.
A preferred tool option in some cases is the cement retainer. This tool prevents backflow during cement setting and formation pressure disturbing the cement cake. A drillable retainer can be set closer to the perforations than a retrievable packer, reducing further the risk of
A variation of the tool-assisted squeeze method is the circulation squeeze. For this method, the squeeze theory previously explained does not apply because the objective is not to form a cement cake or node but to fill a channel or large void behind the casing with cement. The cement slurry is circulated down through the bottom perforations up through to the top perforations back into the casing / work-string annulus, and there is a strong possibility that some of the cement
Circulation squeeze involves some additional risks in comparison with conventional squeeze cementing, with the most important one being the possibility of the working string left trapped in cement. The cement slurry back into the casing could have unpredictable thickening time due to its interaction with a permeable media while flowing up behind the casing from the bottom perforations.
The following precautions should be considered:
• The cement slurry should be low viscosity with very low gel strength for smoother flow (less pressure drop in the channel = less filtration)
• An additional safety factor shall be considered for thickening time. In these operations, the actual thickening time is typically reduced and the gel strength development is considerably accelerated due to the loss of filtrate while the cement slurry flows under pressure behind the casing between the perforations
• Cement slurry volume estimation shall be as conservative as possible.
Cement squeeze procedure
There are two procedures to apply pressure that can be used to maximize the squeeze
Advantages | Disadvantages | |
Running squeeze | + It can be used with cement plug or tool-assisted squeeze methods + Simpler and shorter operation + Requires medium to high injection rate (> 0.5 bpm) + Allows larger cement volumes + More applicable to workover (clean fluids) | + If MASP is achieved sooner than expected a larger than desired cement volume can be left inside the casing + The minimum pumping rate of conventional cement pumping units might be too high + Achievement of squeeze pressure is not necessarily an indication of success + Cement slurry would follow the path of least resistance preventing all voids or leak paths to be filled |
Advantages | Disadvantages | |
Hesitation squeeze | + More suitable for cement plug-assisted squeeze method + Typically for smaller cement volumes + More applicable to low injectivity cases + Gives better chance to fill all voids or leak paths + Achievement of squeeze pressure is an indication of success | + Longer operational time + Job procedure is more complicated and requires + Laboratory tests shall account for hesitation periods + Not recommended for tool-assisted squeeze method |
Running squeeze
During a running squeeze procedure, the cement slurry is pumped continuously until the final desired squeeze pressure is achieved. This squeeze procedure can be implemented either with cement plug or tool-assisted method and the volume of cement is usually large.
Hesitation squeeze
The relatively small amount of filtration rate occurring in low to very low injectivity rates makes continuous pumping with common field equipment at a rate slow enough to maintain a constant pressure below the MASP almost impractical, if not impossible.
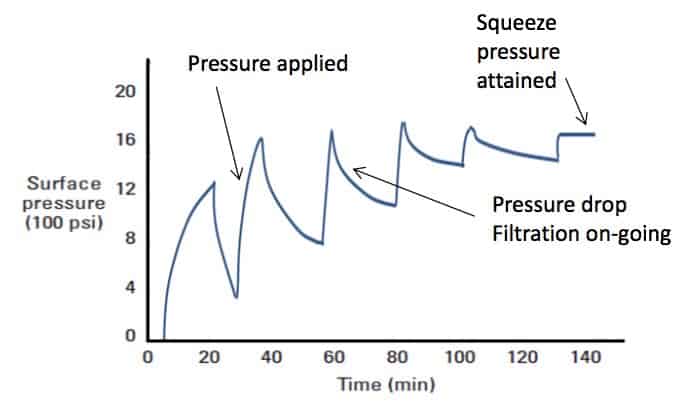
The initial leak-off or filtration is normally fast because there is no cement cake. As the cement cake builds up the filtration rate decreases progressively on every attempt, the period between hesitations becomes longer and the differences between the initial and final pressures become smaller.
Cement Slurry Properties for squeeze cementing
Thickening Time to 70 BC (Bearden units)
Also called pumping time is performed at the estimated bottom hole or treatment depth temperature and pressure using a pressurized
- Test temperature considerations
For squeeze cementing the test temperature can generally (for near-vertical wells, with a known formation temperature gradient) be determined using the API correlation/tables in the API RP 10B-2 / ISO 10426-2, however anytime the configuration of pipe size, depth and displacement rate/time does not correspond to API schedules, Job-specific customized test temperatures and schedules based on actual job parameters and thermal computer models shall be applied.
- Thickening (pumping) time requirements considerations
For squeeze cementing, pumping times shall be long enough to allow the cement slurry to travel to the placement depth, injection of the cement slurry (cement slurry volume at the anticipated injection rate) to the target zone, repeated squeeze-hesitation cycles, plus time to reverse or direct circulate any excess cement out of the well (if this is planned).
The following shall be considered:
- A minimum safety margin of two (2) hours is recommended.
- When testing the slurry for a hesitation squeeze, it
is recommended to simulate the shutdown times in the laboratory during testing of the cement slurry. - An additional safety factor shall be considered for circulation squeeze. In these
operations the actual thickening time can be typically reduced and the gel strength development considerably accelerated due to the loss of filtrate while the cement slurry flows under pressure behind the casing between the perforations.
Free Water
For squeeze cement, free water shall be zero (0%) percent.
Fluid Loss
Fluid loss of the cement slurry is selected based on the injection rate. (see decision tree in cement slurry selection section). Fluid loss shall be measured following the API RP 10B-2 / ISO 10426-2.
Compressive strength test
The compressive strength values are measured following methods and recommendations in API Recommended Practice 10B-2 / ISO 10426-2 section 7. The reference test temperature for squeeze cementing is the hole static temperature at the top perforation/injection point or top of the cement inside the casing.
Other considerations for squeeze cementing
- Conventional cement cannot be displaced into formations as the permeability would need at least to be 100’ Darcy to inject. In case of
micro-cement the permeability of the formation for matrix flow would need to be more than about 25 Darcy. - For cement slurry to reach and fill perforations, channels, or fractures; fluid previously occupying the space is displaced and replaced by cement.
- Cement squeezes will follow the path of least resistance; the squeeze will be unsuccessful unless all the zones to be squeezed are clear and able to accept cement. Success will depend on fluid compositions, solids content, formation properties, existing natural fractures, vugs or caverns, near-wellbore damage, pressure differential and flow rate.
- Once placed, the cement is required to stay in position until it bonds and becomes strong enough to withstand the differential pressure it is exposed to.
- For long term squeeze durability, bonding of the cement is critical; where the target zone is oil
– wet, fluids using surfactants or/and solvents in the first fluids injected could be required.
I hope this information supports your quest for better cementing results; but, if I can be of any help, please do not hesitate to contact me.
Cheers,
L. Diaz
Hola my good friend Lenin. Estaba viendo los tools para squeeze cementing y vi tu pagina. Muy interesante e instructiva. Un Feliz 2021!
Muchas Gracias Ember, un abrazo y exitos. Cualquier cosa que te pueda ayudar me dices
Lenin, Just wondering what you would consider a “large volume” cement squeeze?