This article will provide you with some actionable suggestions for cementing across permeable zones. In previous posts, I have already talked about the effect of formation permeability on the apparent cement presence behind casing, as seen on cement logs. (See: Excellent cement job, but with terrible results … how is this possible?)
Keep in mind that the dominant factor is the loss of filtrate to the formation, as presented in A talk about API Fluid Loss and Mud Displacement, the ‘mystery’ factor in gas and fluids migration. There are two cementing defects typically identified, as described below:
1) Delayed compressive strength development.
This defect is defined as the development of insufficient compressive strength in the cement at the time of running the cement evaluation log, usually 3 to 8 days after the end of the cementing operation. (Much longer than the curing period required to achieve proper compressive strength as per a 24 hr.-UCA reference, for example).
Depending on the length of the section (as applicable to cement slurry volume) and the extension of the permeable zone, I have found this effect to be mainly related to mud properties (fluid loss and viscosity). This leads to lower displacement efficiency before cementing (pre-job circulation – see A talk about API Fluid Loss) and higher while cementing by the cement slurry itself across the permeable zone.
Ultimately, this leads to cement slurry contaminated with previously immovable mud (composed of gelled mud and remnants of thick-porous filter cake) and delayed compressive strength. In a previous experience, the comparison between cement logs days apart helped to highlight this effect (before perforating). However, this is not enough for regulators and company policies to be modified, with the promise of improved zonal isolation in a time when early cement logs appear unacceptable. NOTE: This doesn`t account for the possible contribution of formation movement, e.g., creeping shales.
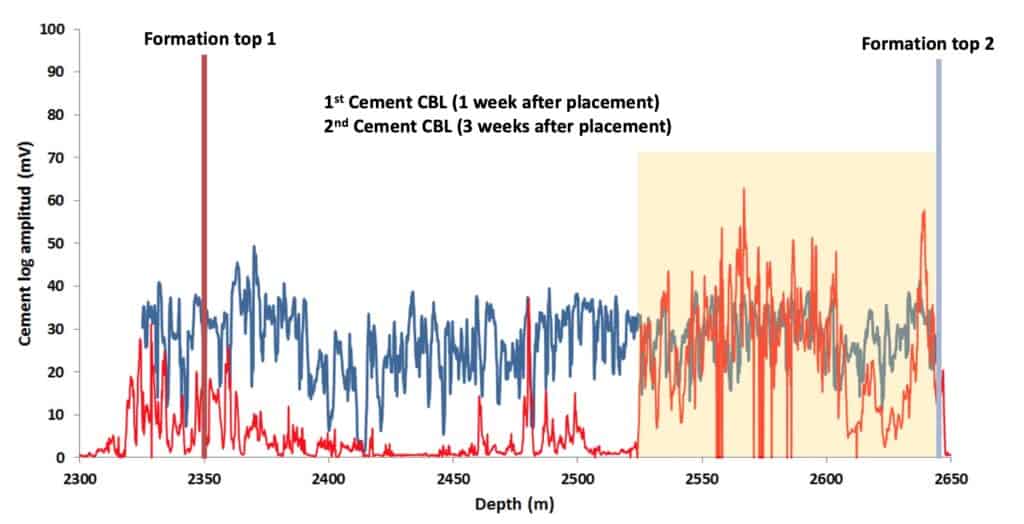
2. High amplitude or “bad cement” across the best reservoir section.
This defect can be defined as very clear deterioration on the cement log, showing almost no cement, across the section of the reservoir with higher permeability. In the previous graph, the red line shows this defect at the bottom of the interval.
Recommended actions for cementing across permeable zones
For cement density in the conventional range, the balance between slurry density and fluid loss control. As cement logs are affected by the compressive strength of the slurry, it is important to implement actions specifically intended to maximize not only compressive strength but also its earlier development. For example, increasing the cement slurry density a small fraction (between safety limits).
This will have a positive effect to mitigate contamination and improved compressive strength. Also, it can reduce the need for high fluid loss control, (most fluid loss control additives have a reducing-negative effect on compressive strength), relying more on dispersion to control the loss of filtrate taking advantage of the lower porosity of the slurry. Keep in mind this recommendation is offered in the context of formation interaction after placement across a permeable zone.
For lower density applications, target low porosity slurry systems.
Proper selection of target thickening time. Understand and manage safety factors that increase the thickening time to prevent their escalation effect creating a fictional or inexistent more severe downhole “well condition”.
For example, the:
- Definition of the BHST itself
- Implied safety factor in the method of BHCT estimation
- Calculation of operational time in liners
- Need and introduction of static periods in TT test
- Long cement columns
- “Round-up” retarder concentration in the field
- Safety factor itself.
Use temperature simulation to assess the wellbore heating schedule after placement to program the UCA and prevent overestimating the 24 hr.-CS UCA value (to derive acoustic impedance reference for “good cement” in logs).
Run a contaminated UCA test, with contamination percentage as per computer simulation.
Use of retarders that offer the lowest gap between thickening time and time to develop 50 psi CS.
Use of fibres in the cement slurry volume, to help minimize the loss of filtrate by reducing the permeability at the cement-formation interface.
Maximize cement coverage using software simulation, from pre-job circulation (displace mud by mud, targeting the risk of immovable mud), mud displacement, channelling prevention to casing stand-off.
Consider casing rotation to ensure cement presence 360 degrees across the interval of interest. Friction exerted on the formation face by pipe rotation has also shown straightening or pore-plugging capabilities lowering the near-wellbore formation permeability.
Really looking forward to reading your comments,
Cheers,
L. Diaz
Hi,
I see this is a few years old, however we are searching for the hydraulic conductivity of cement/grouts being used to seal casings. This post mentions lower permeability zones so wondering if there has been any hydraulic conductivity assessment on cement/grouts??