Let’s have a quick overview regarding bentonite. It is easy to find references online regarding bentonite as a cement extender, the way it works (or I should say reacts), and why additional water is required when using it as an extender. Here I will try to explain as simply as possible, for readers of all levels of knowledge.
First of all, Use the right additive:
I should be precise that not all types of bentonite are good to be used in cement slurry as an extender. There are mainly two types, the Wyoming bentonite, and the beneficiated bentonite. The Wyoming bentonite is the approved one by the API as an extender for cement slurry. At least this is the one that should be used, it is specified as “non-treated” bentonite (API Spec 13A, Sect.5 – Can be found in google).
The other beneficiated bentonite or peptized bentonite, to which polymers have been added to artificially improve hydration is not recommended for well cementing. This one is forbidden because it can interfere with other additives. So first make sure to order the good one.
Additive concentration:
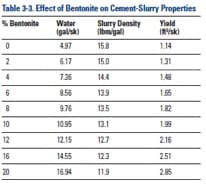
Typical bentonite concentrations used are generally from 1 to 20% BWOC, there are some references stating that concentrations up to 25% BWOC (or even higher in DOBC plugs – gunk plug – for lost circulation/water influxes) have been used. (I never used up to 25% BWOC for primary cementing). This depends on the cement slurry density and properties you are looking for. In general, with bentonite cement slurry densities are from 11.5 to 15.0 ppg.
Bentonite can be mixed in two ways. It can be directly mixed with cement (dry-blended) and later the blend is mixed with water/mix water/mix fluid or it can be mixed in the mix water (pre-hydrated) and later cement is added in the mixed fluid.
It should be kept in mind the following parameters
- 1% BWOC pre-hydrated bentonite = 4% BWOC dry blend bentonite,
- The lower the bentonite extended cement slurry density is, cement mechanical properties will be poor (Table 3-3 and 3-4 taken from Well cementing II edition) and,
- The addition of bentonite to a cement slurry requires additional mix water. A rule of thumb is for each 1 % of bentonite an additional 5.3 % of water is required.
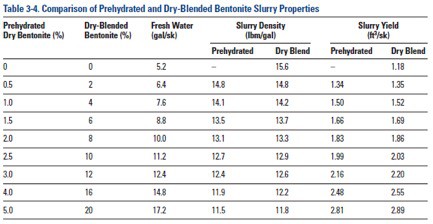
It is recommended to pre-hydrate the bentonite and properly hydrate prior to mixing the cement slurry. Compare to dry-blended, when mixed with mix water (bentonite will hydrate totally in 30 min) properties of bentonite are boosted because it absorbs an important volume of water. But, when it is dry-blended with cement and then added to mix water, it does not hydrate completely (Hydration inhibited by Ca2+ ions in the slurry).
What is the best procedure for mixing the slurry in the laboratory?
The recommended procedure for mixing and testing cement slurry in the laboratory can be found in the API RP 10B-2 sect. 5. It highlights all the requirements (equipment, calculations etc.) and recommendations for testing cement slurries and related material as per simulated well conditions.
As mentioned earlier, for dry-blended bentonite, the mixing procedure in the laboratory is the same as with any cement or blended cement (described in the referenced document). For pre-hydrated bentonite, the bentonite has to be completely hydrated (30 min is required), as any solid additive, in mix water prior to adding cement. Then testing of cement slurry can be performed and completed normally.
Cement slurry preparation or Mixing procedure (general)
- Place the required amount (mass) of mixing water and liquid in the mixing jar or the blender container.
- Start the mixer at 4000 RPM, then add the required additives following the proper mixing order sequence. The additives should be added to the mix water while mixing at low speed. For pre-hydrated bentonite, allow 30 min to ensure that the additive is completely hydrated.
- at 4000 RPM, add the blended cement (cement + dry additive) or cement at a uniform rate in not more than 15 sec.
- place the cover on the mixing container and continue mixing at 12,000 RPM for 35 sec.
- Measure the cement slurry density using the pressurized fluid density balance
Secondly, what about the water requirement as we increase the percentage of bentonite in the slurry?
I add above some tables (taken from the Well Cementing II edition) that can be used as a reference to having an idea regarding water requirement and bentonite’s concentration. This is only as a reference because when designing a bentonite extended cement slurry it is common to add some additional additives as well, such as FL, Dispersant, retarder, etc. So, the water requirement will change accordingly.
Calculations:

To determine the water requirement vs bentonite concentration, if you don’t have a lab sheet or an excel sheet or any other means, you need to do some simple math. The bases are quite simple, I think. You have to know how to determine cement slurry density, slurry yield, the weight of additives and cement sack (94 lb in general, you can find 110 lb too like in Mexico) and parameters like additives absolute volume. You can have a look at the Well Cementing book II edition in appendix C – Cementing calculations to have a better idea, here is an example of calculation provided as a reference.
Software:
Another way to do that could be, this is probably the simple one, is to use some ‘’free software’’ like eRebookTM (Halliburton) and I-handbook (Schlumberger). Both are free and can be downloaded online.
I am sure that there are cementing calculations’ sheets online that can be used too, probably some additional online researches are required. However, the recommendation will always be to go back to the book (mentioned above) to understand the basic calculations and concepts before using the software. Remember, the software will give outputs based on the inputs provided. There are some pictures presented below as references.
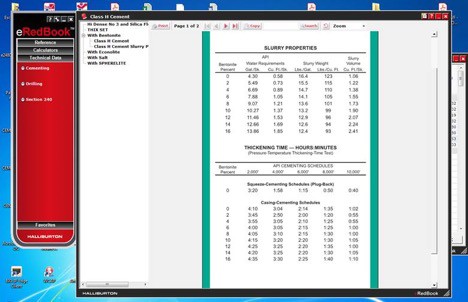
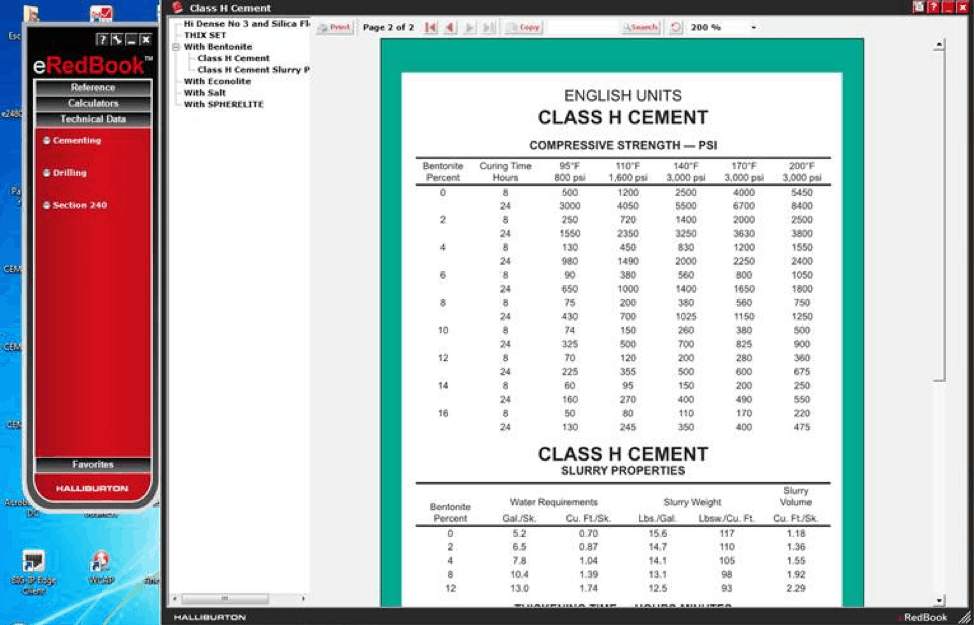
Print screens from eRedbook
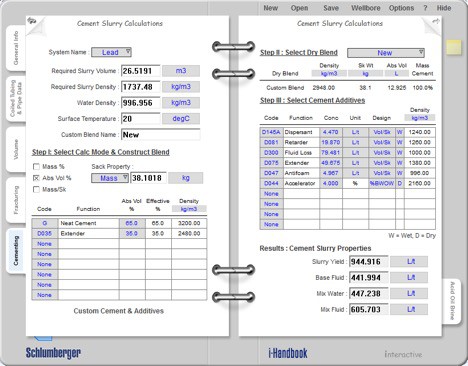
Print screens from I-handbook
I hope that this summary has provided some answers to your questions. Feel free to contact me if any additional information is required. I will be more than happy to help if I can.
Best regards
L. Bikouyi
The lab mixing of bentonite is effected by the less aggitation. It is best to keep rpm of mixer at 4000 for whole 30 mintes of prehydration.
On field make sure bentonite is added via hopper (if it is wet blended) and prehydrated in the batch mixer for at least 30 minutes.
Thanks, Mubashir,
Prehydration of bentonite is very important and a key element to ensure the final properties, some companies even include a QA/QC step after bentonite is prehydrated (measuring funnel viscosity) before adding the weighting agent. The process becomes a bit more difficult to control if the rig pits are used as it includes other variables to consider (cleanliness of tanks, prevent leaks in valves, getting proper agitation, etc). The spacer quality is underestimated sometimes, but it is fluid that must comply with density and rheology requirements in the job design.
Thanks again for your input Mubashir
Cheers
L. Diaz
Hello Lenin,
– On location after mixing bentonite with water on tanks and for some reasons the job delayed for a couple of days, is it recommended to keep the mix fluid in circulation to ovoid settling or we keep it on static?
– Sometimes after finish a bentonitic job, found a huge amount of Bentonite on bottom, what are the reasons?
Thanks
Hi Moussa, thanks for your questions and for reading my blog.
The situations you are mentioning are not uncommon, and their occurrence can be due to several factors, mostly operational and/or materials related.
Regarding your first question, yes it is recommended to keep circulation and agitation (if available) to avoid settling. This will help to maintain bentonite’s and other polymers (if any) suspension capacity and/or the weighting agent in suspension. Nevertheless, settling will occur and keeping the fluid in motion, adding mixing energy, is mainly a mitigation measure. This is particularly true if you are using rig tanks / pits where circulation is not that efficient. The best thing is to add the weighting agent when the job is confirmed. I am assuming you are talking about a cementing spacer.
Now, in terms of settling, I am mainly referring to the weighting agent and that the bentonite was originally properly hydrated.
The main reason for settling in summary are:
1) Insufficient hydration of the bentonite due to insufficient mixing energy (in terms of intensity and duration of mixing)
2) Low-quality bentonite with addition of other non-bentonitic viscosifiers
3) Improper addition of the bentonite, leading to flocculation
4) Post addition of other liquid chemicals like surfactants, if required for reverse emulsion or wettability
Now, finding settling of bentonite is a bit odd, but it can be due to low-quality bentonite or the quality of the mix water (basically salinity content)
Cheers
L. Diaz
Nice article, reminds me years ago doing the absolute volume calculation and the pre-hydrated bentonite sometimes can be become tricky…
Thanks a lot for your comment Novrendi,
Cheers
L. Diaz
Thank you very much for the write up ,,got a lot from it but I want to ask ..in a situation where one is asked to carry out a detailed explanation on determining the thickening time of cement / bentonite at different temperatures…what should be the right procedures?
Hi Ladi, thanks for interest in proper well cementing. The procedure is detailed in API RECOMMENDED PRACTICE 10B-2 for thickening time. In this case, it will require a test for each temperature. Hope this helps, if not please let me know at my email dlenin@hotmail.com
Cheers,
L. Diaz
Hello what about adding bentonite to control fluid loss/free water (in cement + bentonite + water lab set up) should the 5.3% extra water be added or bentonite should be added without the water ?
Thanks
Hi Ibrahim, bentonite was certainly considered a fluid loss control material in the early days. The main reason for using bentonite pre-hydrated (in the mixed water) is to use less amount of it. It will also, depending on the quality of the bentonite, produce better effect on the slurry, more stability and better reology. When mixed pre-blended, it won’t have the chance to hydrate completely, because both cement and bentonite will be competing for water, that is why it is added more to achive a similar effect.
Cheers
I see contractors suggesting using API 13A Section 9 (Sodium Bentonite) Polymers as a substitute for API 13A Section 4 (regular Bentonite) in a cement bentonite slurry wall mix. Is this acceptable? What are the differences, pros and cons?. Let me know if you get a moment. Thanks.
I always suggest to locally test all bentonites available, to see the effect on the particular slurries
Very rarely you will find the bentonite recommended in the cement literature available, unless it is sourced by the cementing company
Cheers
Hello , i cannot find the mixing procedure of bentonite in API , can you please advise where can i find it
Below a reference to a procedure normally used:
Verify the rig pit#X used with the mud engineer and the derrick man and confirm dead volume (dead volume xxbbl)
Make sure that the lines to and from the pit, and the pit itself are clean.
After all isolation valves are closed and checked, fill the base fluid into the pit.
Measure the chloride content of the fresh water and report. Measured value should be below 1000ppm
Start preparing the fluids according to the procedure below, only after confirmation from drilling supervisor
Add antifoam into water and disperse thoroughly by circulating the mixture and with centrifuge and paddles on.
Add polymer with the help of a hopper (Plan for 30 minutes hydration before adding bentonite as per lab test)
Add Bentonite with the help of a hopper (Plan for 30 minutes hydration before adding barite as per lab test)
Dear Sir,
I really appreciate your doings with Bentonite, Cement and Water.
Thanks a lot, it helps me a lot.
Samuel B
Not a problem Samuel
Cheers
Good morning,
we have a project that will be using bentonite (API 13A Section 9) and processing through our dry concrete portable plant.
Do you have any suggestions on the sequence of loading the various materials?
Our design per yard is:
Cement = 110 lbs
Slag = 441 lbs
Water = 265 gal
Bentonite = 100 lbs.
The article explores the role of bentonite in cement slurries, highlighting its benefits like improved viscosity, suspension stability, and reduced permeability. Bentonite is used in oil well cementing to enhance fluid loss control and provide flexibility in challenging formations. The piece discusses types of bentonite, their application processes, and compatibility with additives for optimal performance in cement systems. Concrete Company Goodyear