I know that there is no need to remind you of the objectives of a cementing job but, to be in context, let’s mention some of the main ones such as:
- Providing zonal isolation
- Structural support for the wellbore
- Casing protection against corrosive fluids.
Failing to meet these objectives could potentially have consequences, in terms of wellbore integrity, during the well’s working life.
Achieving effective zonal isolation with cement requires the cement slurry, teaming up with (a) non-cementing fluid(s) ahead, (spacer, pre-flush or both) to effectively displace the drilling fluid (mud) in the annular gap (a complex environment). If the mud is not well displaced, or non-cementing fluids are left behind in the annular; the cement is contaminated risking or undermining its performance as a barrier element.
One of the main causes of cement failure is contamination. A contaminated cement slurry has its properties affected producing; impaired compressive strength (CS) development, shortened or delayed thickening time (TT) and/or cement gelation, for example. Contamination occurs when the cement interacts with mud, which can occur in dynamic and/or in static conditions because both fluids are incompatible mainly OBM or SBM (with WBM it depends on chemical composition). For that reason, fluids like spacers and wiper plugs are used as measures to help prevent and/or mitigate these interactions.
The first purpose of spacer is to prevent cement slurry from interacting with the drilling fluid and it also helps with mud displacement. They are carefully designed, they are compatible with both fluids (mud and the cement slurry), their chemistry should be able to clean solid surfaces and leave them water-wet and they should not damage the formation. Nevertheless, spacers are additional fluids pumped and their interaction with cement may also alter somehow cement slurry properties. For that reason, bottom plugs are used. They help to prevent the fluids to intermix and to assist in cleaning the inner wall of the casing
The combination of both (spacer and bottom plug) has shown to be effective and efficient in primary cementing jobs. However, the way it is used may vary from one location to another, from an engineer to another and from a best practice to another one. In summary, some prefer to pump the spacer before the bottom plug (cement slurry – bottom plug – spacer – mud) and others after the bottom plug (cement slurry – spacer – bottom plug – mud). Which from both options is the best way to pump the job in the most effective manner to have the best results?
I hope that this post will help me to collect more information regarding this topic and shape my understanding, for now, I would like to share my thoughts on it and please feel free to provide feedback.
Background – Where did this topic come from and why?
Recently, I had the opportunity to review a 16’’ casing cementing job program from a cementing services company and something particularly called my attention to the fluids’ sequence; the spacer was programmed to be pumped after the bottom plug (cement slurry – spacer – Bottom plug – mud). I did request some technical reasons or guidelines or any documented best practices to understand why they planned the job in this sequence. They did provide some arguments but I was not so thoroughly convinced, and then I found one interesting.
Among all the reasons provided, the most important was to prevent spacer contamination with mud before reaching the annular. They claimed that while traveling down in the casing (bottom plug – spacer – mud) the spacer loses its performance due to the contamination with mud, and despite the potential contamination with the cement slurry, still conserving its most important features (depending on volume) if pumped after the bottom plug (spacer – Bottom plug – mud). Very interesting, isn’t it? I reviewed some of their previous jobs designed and performed, I realized that in all the jobs, except the 30’’ conductor and the 20’’ surface casings, the same sequence was used. Unfortunately, cement evaluation logs were not available.
To be honest, this is not a technique that I used to use, I should say that I’ve never used it. The way I learned, designed and performed jobs, always being: bottom plug – spacer – mud. So, instead of being surprised or “offended by such an atrocity” being an open-minded person, on the contrary, I was more curious about it and certainly needed to understand why and find meaningful answers.
Cement spacer function / contamination
Spacer fluids are pumped not only to ensure that cement slurry is not contaminated with mud but also to ensure good mud removal. It is designed following the density and rheology hierarchy concept between those of the drilling fluid and cement slurry, this has shown to be effective and helpful with mud removal. Under optimized (spacer rheology, density, volume, etc.…) design’s conditions it does its job and helps to displace mud in the annular.
However, this concept of density hierarchy may work fine in annular but presents some details when fluids trip down in the casing. Normally, flow in a pipe is laminar – the particles in contact with the pipe wall are stationary vs the particles at the center of the channel moving at the greatest velocity. When there is no mechanical barrier, in dynamic conditions (pumping down in the casing) it is normal to see high-density fluids falling through low-density fluids; cement through the spacer and/or spacer through the mud. Reducing density difference somehow helps to mitigate this effect. In practical terms, fluids intermix while traveling down in the casing and this is well explained when you start reviewing fluids’ contamination. By the way, it is well detailed and explained in the case of cement plug placement since it is one of the main reasons for cement plug failure.
The contamination of the fluids while traveling down are enhanced when:
- The fluid velocity/flow is in laminar flow. Laminar flow is more favorable to fingering than turbulent flow.
- The string/casing ID is larger and the well is deviated.
- The density difference is important (inertia forces & fingering effect). Cement falls through the spacer/ mud or spacer falls through the mud, heavy fluids falling through lighter fluids & a mud cake (film) left on the inner wall side of the casing). This also applies for rheology.
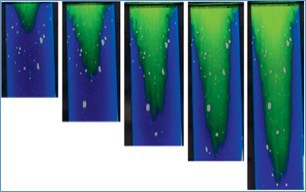
This is to say that fluids intermix (cement/spacer or spacer/mud) before reaching the annular, once they reach it they may not be as effective (their properties in a portion of their volume altered) as they should be. To prevent that to happen the bottom plug is used. The bottom plug helps to prevent fluids intermixing and wiping the casing to clean its inner wall (remove the mud film). The most important function is to prevent the fluid from being contaminated by another. When referring to spacer fluid, we may wonder, does it change something pumping the bottom plug before or after the spacer ahead? What is the best or right position of the bottom plug in the pumping sequence?
Case 1: bottom plug – spacer – mud:
Let us have the image in Figure 1 in mind. The mud contaminates the spacer while it travels down inside the casing (falling through the mud) and in the end, the mixed fluid (mud–spacer) will, in turn, contaminate the cement slurry once it starts flowing in the annular. The contaminated spacer may lose its properties and performance before reaching the annular, at least this is what the services company claimed and pretended to avoid. However, this is where the importance of rheology and density differences, compatibility tests, and spacer chemicals and others take place. It is designed to be compatible with mud and to remove it.
In addition, in the cases of long strings (16’’ to 5’’), another factor helping here is the fact that important volumes of cement slurries (lead cement slurry in general) and spacer (I should say optimized volume) are pumped. For example, the cases of production casings (from 7 5/8’’ to 5 ½’’). Probably, depending on desired TOC and annular gap, large volumes (spacer or cement) are not pumped as it is in larger casing diameters and we are still getting good results despite the expected contamination, but I think we may see it with a different approach. What I mean is we should see it in terms of % or casing capacity/volume pumped ratio. Example in a 5 ½’’ production casing up to 1500 – 2200 m, pumping 40 – 50 bbl of the spacer and 40 – 50 bbl of lead slurry vs 120 bbl casing capacity (small casing ID). This is > 65% casing capacity (without mentioning annular capacity), right? I think it does help.
In the case of liners, the above mentioned is also applicable. I should not generalize here. In this section, I would like to specify that I am debating on the case when the double plug system is used (like in the offshore environment) to maintain the variable since our post related to the spacer and bottom plug. In liner’s operations, particularly the production’s ones, where the cement volume is small and contamination risks are high, the volume of the spacer is also increased.
Please note that talking about spacer volume does not mean that I want to deny all the work done to optimize the cement placement, all the software and simulators technologies available to optimize the design and guarantee that fluids don’t intermix during the job, because the goal here is not to review all of these aspects but spacer position.
To sum up, using this sequence, as presented in the literature (documented best practices, technical papers, and experiences), has helped and still helps to achieve excellent results.
Case 2: spacer – bottom plug – mud:
A similar effect is expected as presented above regarding contamination while traveling down inside the casing. However, in this case, having the spacer after the bottom plug, the spacer contaminates the cement slurry and at the end, the mixed fluid (cement – spacer) will, in turn, be contaminated by mud once it starts flowing in the annular.
When the bottom plug is located before the spacer, it will probably help to maintain the spacer properties, however, to maintain its properties we have to assume that cement does not move through or at least, it will do but with less impact, due to the fact that density difference between the spacer and lead slurry is not too high sometimes. Again, as for the first case (bottom plug – spacer – mud), pumping large volume (long string case) and particularly in this case the cement slurry surely helps.
The main concern here may be how pure the cement slurry reaches the annular. I guess in the case of long casings it is ok since the volume is huge and only lead cement is exposed to contamination. But what about jobs where reduced volumes are pumped such as production liner cementing job or 5 ½’’ casing cementing job (as per the example is given above)?
The problem with liner cases (when a double plug system is used), more specifically the production casing, a single cement slurry is used and not only the volume is small but also the density difference is quite important (single slurry vs spacer). These two factors, I think, increase the probability of having the cement slurry falling through the spacer and getting contaminated before going to the annular.
Let have an idea from software/simulations
In general, simulation’s outputs are more focused on cement placement evaluating how it travels inside the casing and in the annulus. Sometimes the mixing and fingering inside the casing are ignored or not well presented in some software, probably because it may be considered that they are less drastic than the effects observed in the annulus which is, by the way, a more complex environment if we have to compare. Ok, let close this parenthesis, what I am trying to highlight is the fact that maybe we really don’t pay attention to spacer contamination while tripping down. I am sure, each engineer surely has a personal answer or view to that.
For those who are curious, I did the exercise. For the simulation I used the spacer as cement slurry and all the cement slurry as a spacer, then I simulated evaluating, particularly while tripping down inside the casing. The results are quite interesting; first, it confirms the high of spacer’s contamination before reaching the annular independently to the position of the bottom plug. However, there is a difference in both results, of course, due to the nature of the contaminant (mud or cement slurry).
What is your preference?
In the first case (Bottom plug – Spacer – Mud) the spacer is mixed with mud and the cement slurry reaches the annulus uncontaminated (100% of its properties). This only confirmed what was claimed by the services company, but in reality, this is well known and this is one of the reasons spacer volume is increased and compatibility tests (API RP 10B2) are run between spacer and mud to inhibit any unpredicted interactions that may interfere with the spacer’s performances (optimizing its formulation/design – rheology, density, etc.).
In cementing jobs where huge volume is used there are no big issues, of course, all tests have to be run. In general, the lead slurry (first barrels) will be contaminated with the mixed fluid in the annular. With appropriate software, percentages of contaminations can be estimated and tests like CS can be run to determine its final value. Ok, honestly, there is no need to do that for lead slurry unless unexpected well conditions or some high-profile liner jobs (HPHT 9 5/8 or 7/8 liners for example) required such tests and more. However, in small volumes (liner’s jobs), the same exercise with software should be done and the required tests run (there is a post on that in this blog).
In the second case (Spacer – Bottom plug – Mud) the spacer is mixed with cement slurry and it reaches the annular already contaminated (not at 100% of its properties). This can be a real issue, more with small volumes (production’s liner jobs) than with huge volumes (long strings). All the tests (API RP 10B2) have to be run between fluids of course, which include rheology, TT and CS tests. Allow me to focus on CS in this post assuming that the other two are well known.
The information about how the cement slurry’s CS is affected when cement is contaminated with mud is available in the literature. This is a well-known case (as well as all the impacts). However, what about the mixture of cement/spacer? Instead of going through the literature let me describe a practical case.
The last case I faced with the mentioned local services company was a production liner at 4800m. They were planning to pump the job as per their practices as per the following sequence: Drop the first dart + 60 bbl of spacer + 35 bbl of cement slurry + drop the 2nd dart + displacement (spacer and mud). To avoid any unnecessary arguments, I requested to run simple CS tests with cement contaminated with spacer at 10 and 30%. The results are presented in Table 1.
Mixture fluid | 100% cement slurry | 90%/10% cement / spacer | 70%/30% cement / spacer |
CS 24hrs | 2202 | 1894 | 1240 |
CS Reduction (%) | – | 14% | 44% |
Table 1: 1.90 g/cm3 cement slurry (blend Class H + 32% Silica Flour + 3% Micro-silica + the required additives)
Table 1 is telling me that the more cement is contaminated with spacer, the less CS is developed in 24 hrs. It is clear that, depending on the contamination degree of our 1.90 g/cm3 cement slurry, the slurry will be placed in the annulus with less CS than the original design before interacting with any % of mud (expecting that it will set).
From the results obtained, the decision was clear and additional tests, as tests with a mixture of 50% of the spacer or a mixture of 30% spacer/y% cement + x% of mud, were not required. At that moment, I think, they were not necessary because it was clear that a mixture with mud would have probably given less CS. Again, this depends on fluids (spacer and cement slurry) types and designs, results can vary a bit from a design to another but at the end, the CS will drop considerably, the same works for the MRayl value as well (the right value should be provided for the cement evaluation logs).
Cementing job evaluation:
It would have been interesting to comment more comparing CBL VDL logs from both cases. Unfortunately, data are not available since the final client does not run logs to evaluate the jobs. And if he did, according to some comments from local engineers on both sides (final client and cementing services), logs would have been run after a week or more like a month. A month is a quite long time indeed, but CBL VDL logs used to be run, especially for production’s 7 o 7 5/8’’ liners, after the last 6 ½’’ section was drilled. The common practice was to run CBL VDL + Caliper and any others at the same time. This is to say that after such time probably the log’s responses may be the same, except if the calibrations are not done properly as per the correct MRayl value.
Let me close my thoughts
The spacer and the bottom plug play an important role in cement placement and help meet the job objectives. In this post, we attempted to explain that it is not all to use a spacer and wiper plug to meet job objectives, their position is also a critical parameter to be considered. For now, I would prefer to pump the bottom plug preceded by the spacer ensuring that the cement slurry at least will reach the annulus uncontaminated because its interaction with the spacer alters its properties.
Cementing jobs are performed almost everywhere a well is drilled (oil and gas, geothermal, water, gas storage, salt production, etc.…), the probability to have more data to sustain the practice implemented by that service company, I think, maybe high. I am sure that there are undocumented best practices developed and implemented somewhere and it is unfortunate indeed, we don’t have more data on this topic. What I am expecting now is to have some feedback and experience from readers. Please share with me I will be more than happy to read and learn from you all. Let’s open a new discussion and share.
Regards
L. Bikouyi
Some references to read
- Gabard, C., “Déplacements de fluides miscibles non-newtoniens en conduite cylindrique verticale”, PhD thesis, Université Paris VI, Jan. 2001.
- NAKAYAMA Y., “Introduction to Fluid Mechanics” Former Professor, Tokai University, Japan, UK Editor R. F. BOUCHER Principal and Vice-Chancellor, UMIST, UK
- Beirute, R. M. and R. W. Flumerfelt, “Mechanics of the displacement process of drilling muds by cement slurries using an accurate rheological model”, paper SPE 6801 presented at the 52nd Fall Technical Conf. And Exhibition, Denver, 9-12 Oct. 1977
- Fluid Flow Fundamentals https://www.slb.com/~/media/Files/resources/oilfield_review/ors96/win96/12966164.pdf
- Nelson E. B., Guillot D., “WellCementing”, 2ndEdition, Schlumberger. 2006.
Thanks Bikouyi , it is very intersting topic .
Thanks Bikouyi, very interesting topic.
I’ve worked for six years in Venezuela east with HPHT and shallow wells, we always use spacer /bottom plug /mud. I’ve always read in all books the other way but, in the service company I work, they say the same you find out: spacer would saturate and wouldn’t be effective at the annular, so is difficult to evaluate since in Venezuela never runs CBL and we have done many good jobs and some ineffective ones, I think could be a good thesis. However, after reading your analysis, the Bottom plug – Spacer – Mud technic seems to be the ideal recommended practice, and I should use it firstly in liners because of the small slurry volume but in another hand, the CS is not badly affected regardless of the spacer-slurry contamination, >1000 PSI of CS is enough for hydraulic seal and casing support. I think all here is about college engineering and field engineering. Best regards…
Thanks for your input,
My recommendation before introducing a change in fluids sequence and position of mechanical barriers is to evaluate the effect of cement placement and properties. In today’s world, We cementers have access to better software simulation tools that allow a prediction of contamination of fluids; this is a mandatory first step and then using that output perform laboratory tests, which are going to include rheology compatibilities, contaminated TT and CS. In some cases, like liners using double-dart systems, tests like go-no-go and SGSA might be required to asses the behavior of the mixture above the LH. In Liners the risk of gelled by-products above the LH increases with temperature and depth.
Cheers
L. Diaz
i have quotation
a) Discuss the basic characteristics of spacer used in the oil well cementing operations.
b) Explain the main parameters measured when testing a cement slurry and cement rock
c) A 600-ft plug is to be placed at a depth of 8,000 ft. The open hole size is 61/2inch, and the tubing size is 2 3/8-in. OD (4.6 lb/ft). 10 bbl of water are to be pumped ahead of the slurry. Assume a slurry yield of 1.18 cu ft/sack.
Calculate:
i. The number of sacks needed for the job
ii. The volume of water to be pumped behind the slurry to balance the plug, and
iii. The amount of mud required to displace the spacer to the balanced point.
Hi Mohammed, thanks for your contribution. Please take a look at this post for the balanced plug calculation You can also receive the Excel sheet calculator.
Regarding a) and b) I will soon write posts to cover these topics. Thanks
Cheers
L. Diaz