In the past, I have written extensively about plug cementing, perhaps more than any other topic on this website, and the reason is simple: cement plugs are challenging. In my case, my eyes started to open back in Mexico while attempting deep sidetrack cement plugs.
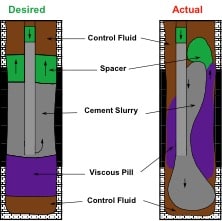
An SPE resulted from that trauma in Mexico after we finally got it under control, bringing success rates up to 100%, almost inconceivable before our time. After this experience, each time in every part of the world, in any operating environment and independently of the well’s purpose, objective, or condition, I have taken cement plugs very seriously, more than any other job type. And simply because I want to do just one! Get it right the first time.
A summary of cement plugs guidelines for drilling and workover is already available on this website, as applicable to the main reason for failure:
- Cement slurry contamination during placement, inside the tubing or DP, at the front and/or rear interfaces. Mentioned in Actions to prevent contamination and liner cementing, as applicable to in-pipe interface mixing.
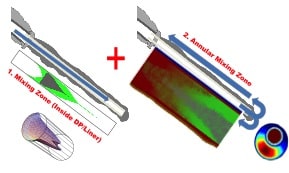
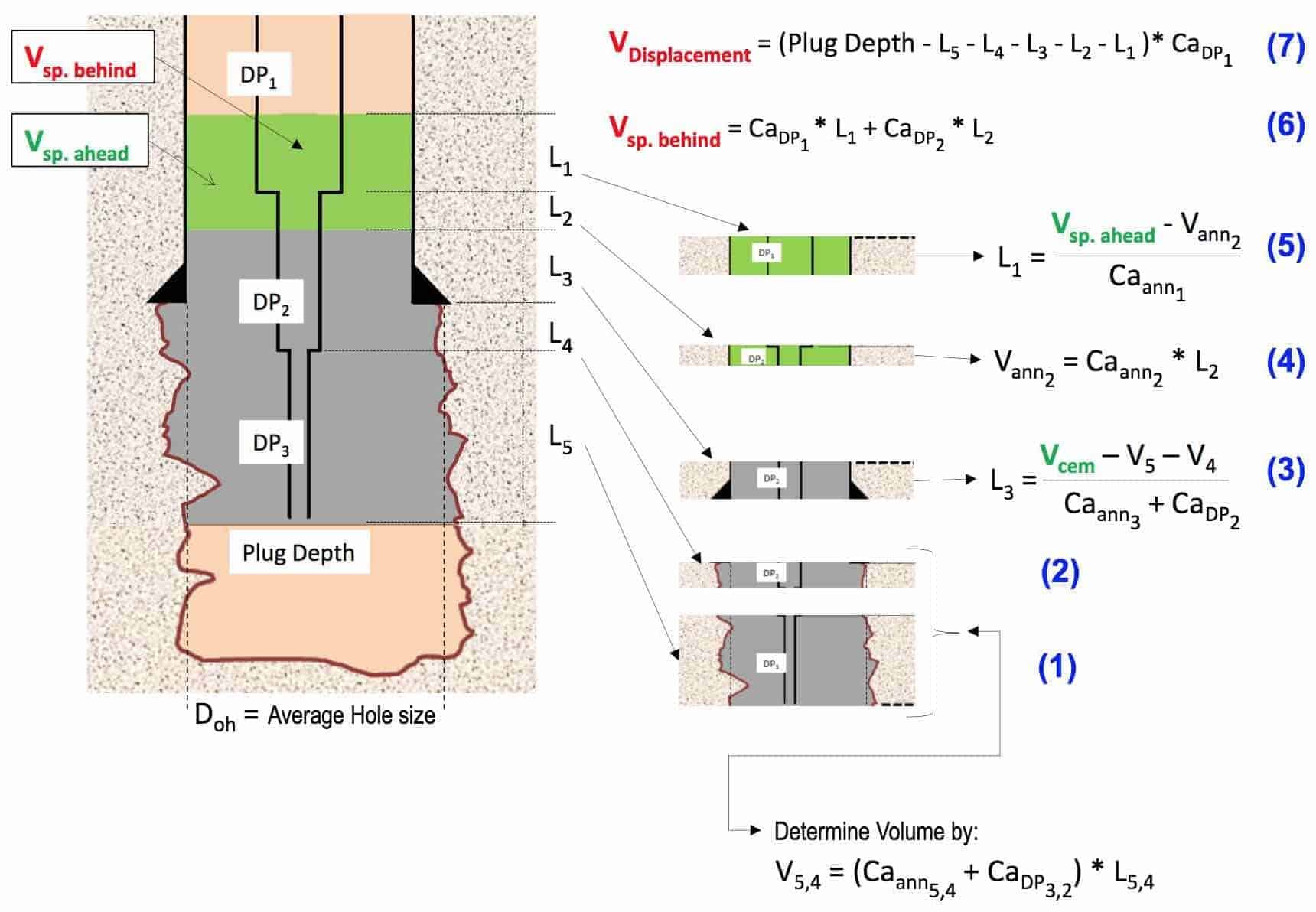
- Pulling out of the hole too fast, swabbing while POOH or unknown hole size (OH).
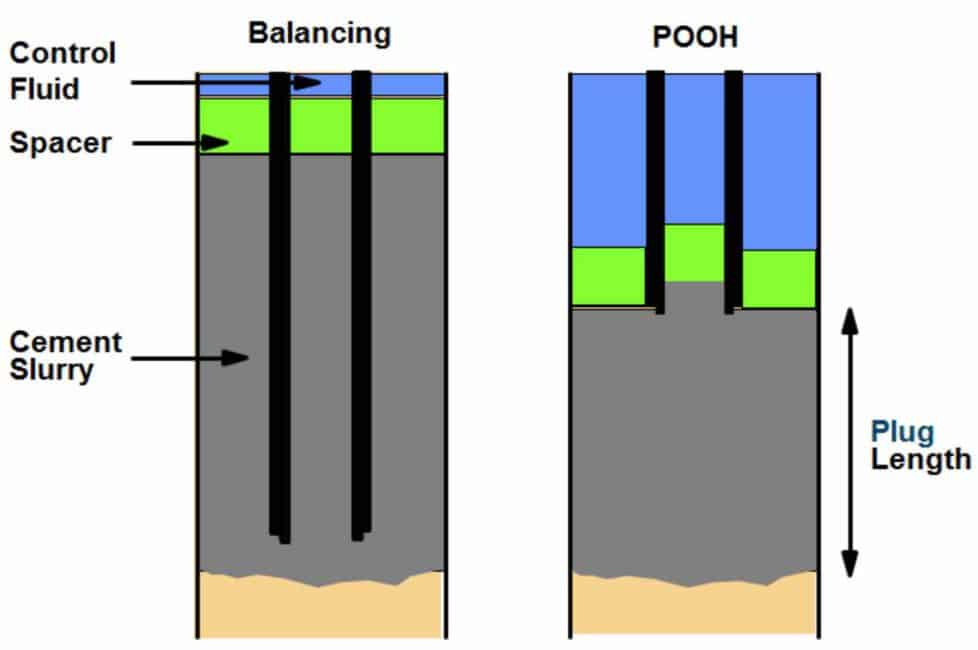
- Unstable cement plug base.
- Place a hard base, like a bridge plug.
- Cement density > pre-flush / spacer density > control fluid
- Viscous pill as a base (require proper design)
- For low density brines, the pre-flush can be water.
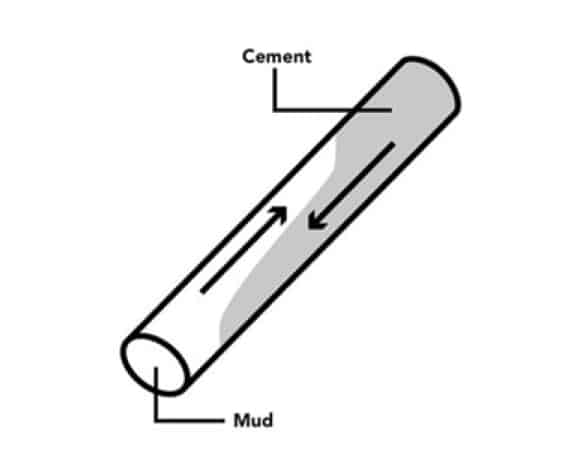
Assuming the slurry is designed correctly using the right reference temperature, overall, the main issue is contamination.
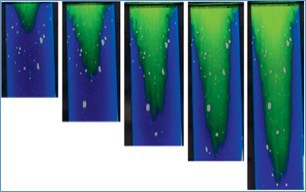
That is why longer WOC and careful tagging/circulation are acceptable mitigations, however with an associated cost: extra time, but always better than repeating the job.
NOTE: This post only covers cement plugs positively affected by gravity. See https://better-cementing-for-all.org/highly-deviated-and-horizontal-well-section-abandonment for horizontal cement plugs.

In general, cement plugs job complexity is related to hole size, depth, and wellbore fluid. For example, the bigger the hole diameter, the more difficult it is proper placement and achieve plug stability or avoid sinking for off-bottom plugs. The risk of higher in-pipe contamination for deeper plugs, and finally, the nature and density of the wellbore fluid (high density, OBM, or WBM) worsening the effects of contamination or low density like completion fluids and brines becoming an issue to avoid sinking or slurry acceleration in the high salinity environment.
The good thing is that failure will only be predominantly affected by one variable, it would be either hole size, depth, or wellbore fluid. Understanding this is important to identify where to address design and prevention efforts. Remember, getting the cement plug right the first time.
In all my previous posts, however, I have not spoken about the use of tools. I have mentioned mechanical separators (more useful for plugs deeper than 3000m), but never actually really talked about placement aids, like the plug placement tool or the cement support tool.
Coming up, I will be dedicating individual posts to these two tools in particular (Part 2 and Part 3). Here I prefer, rather than talk about my own experience with these, to reach out to the best companies around providing these services for more information and a description of their experience. However, you will have the chance to comment, support, or challenge the content in these future posts with your own knowledge. I am pretty much looking forward to this discussion.
Cheers
L. Diaz
It is match better for horizontal wells to spot small cement plug as a hard base and tag it before spot the cement plug insteadoff using DHT.
Also using diverter perforated sub with closed end to breake the fluids on the end of tbg or DP reduce the contamination.
Thanks Ali for sharing your experience.
Both of the practices you mention are legit and can provide solution in the applicable cases
Cheers
L. Diaz
Lenin its nice and one of the sensitive issue aa far as Drilling Engineering is concerned. With my experince few of the following points / comments I would like ro mention.
1. In case of KOP or any cement plug with partial return scenarios, it is always essential to have solid base like BP or strong high viscous pill to place a strong cement plug, but in many cases where the strong base is not able to provide the cement plug sagging or interface contamination may takes place which leads to not to having desire TOC. My suggestion in this regard a. Keep the viscosity of the pill min up to 150 ppb or more and b. Keep the plug under pressure after placement (500 to 600psi) depends upon well condition in order to get good compaction, helps to avoid contamination severity and probability of getting hard desired TOC in first attempt.
2. In case of severe or complete loss condition, its very difficult to give assurance for first attempt success but with proper well data, actual formation data and with proper chemical composition and technique you may go close to perfection in first attempt.
Hi @Pushkaraj Altekar, thanks for your excellent recommedations very applicable.
Perhaps, just to mention from my experience, KOP meeting two objectives, cure losses and support for side-track, is sometimes a bit ambitious. In deep wells this a big concern due to the long trip times (POOH and RIH) or even worst in case of very hard formation.
Hi Lenin,
Thanks for this interesting article, indeed it is very important to achieve a successful cement plug from first attempt to save rig time and to reduce the consumption of cement materials. I have few points for discussion here;
1- We always need to remember that cement plug recipe will be different for mud losses treatment from abandonment purpose. In mud losses scenario we will design the plug to be easily drilled to avoid sidetracking the well and restart the losses problem from zero. While in abandonment or sidetrack I will design the plug with enough hardness to achieve efficient isolation or sidetrack the well.
2- During my career I saw many cementers rely on densimeter when pumping the cement slurry, in my opinion we always need to confirm the densimeter accuracy by measuring the slurry density using the pressurized mud balance, at least 3 times during pumping or every 5-10 minutes depend on estimated job time.
3- It will be appreciated if you explain your thoughts whether you prefer to position the OEDP at top, in the middle or at bottom of the loss zone to spot the plug? Personally I prefer from top in case of complete/sever losses, and from bottom or in the middle of the zone in case of partial mud losses.
4- Also for cement plugs with lengths of more than 250 m mostly for abandonment we can do it as back to back plug (split the plug to two plugs), we pump the first plug and WOC then we go and tag first plug to pump the second one. Let me know if you advise a different technique.
Regards
Dear Methane, only for this comments and evidence of experience, I can see you had a very nice career. I know, I was a witness for some time. Please be sure to extend all this knowledge to younger engineers and as usual if I can be of any help please do not hesitate to contact me
All the best my friend
Very useful and interesting article, Lenin; I would like to know if any additives related to casings/liners corrosion inhibition are added to cement, or the casings/liners corrosion is mitigated only by the alkaline environment of cement. What is the typical pH of the cement mix?